10 Tips for Successful Packaging: The Key to Impressing Your Consumer
Juan Carlos Cuevas • 7 de febrero de 2024
Packaging is not simply a wrapper; it's the first impression consumers have of your product, whether it's Food Product or Pharmaceutical. Successful packaging not only protects the product, but also tells a story and creates a connection with consumers. In this blog, we'll explore the 10 key tips to ensure that your packaging is not only functional, but also stands out and attracts your customers and consumers.
1- Know Your Audience: Before designing packaging, it's crucial to understand who your product is intended for. Research your audience, their preferences, and values to create packaging that resonates with them.
2- Attractive and Coherent Design: Packaging design should be visually appealing and consistent with your brand identity. Colors, typography, and graphics should reflect the essence of your product and attract the attention of consumers on the shelf.
3- Functionality and Protection: Don't sacrifice functionality for aesthetics. The packaging should protect the product effectively and be easy to open and close.
4- Sustainability: In today's era, sustainability is key. Consider using environmentally friendly materials.
5- Highlight Your Strengths: Identify the unique aspects of your product and highlight them on the packaging. Whether it's product quality, special features, or unique benefits, make sure your packaging communicates those features and benefits clearly.
6- Clarity of Information: Key information should be easily readable. Clear and informative packaging builds trust with consumers.
7- Market Testing: Conduct market testing to gauge consumer response before launching your packaging on a large scale. This will allow you to make adjustments based on your audience's preferences.
8- Continuous Innovation: The market evolves, and so must your packaging. Stay on top of trends and look for opportunities to improve and maintain the freshness of your product in the market.
9- Unboxing Experience: The experience of opening the package can be just as important as the product itself. Create a memorable experience with an engaging unboxing that excites your customers.
10- Feedback and Continuous Improvement: Finally, collect customer feedback and use it to constantly improve your packaging. Adaptability is key in a dynamic market.
In the competitive world of commerce, successful packaging is essential to stand out from the crowd. Follow these 10 tips to make sure your product not only reaches consumers, but also makes them fall in love with it from the first glance. At Plasscon we have a team of engineers and technology for the creation of projects and development of specialized products for the Pharmaceutical, Food, Cosmetic, and Home industries. Contact us for more information. Let us support you in your project.

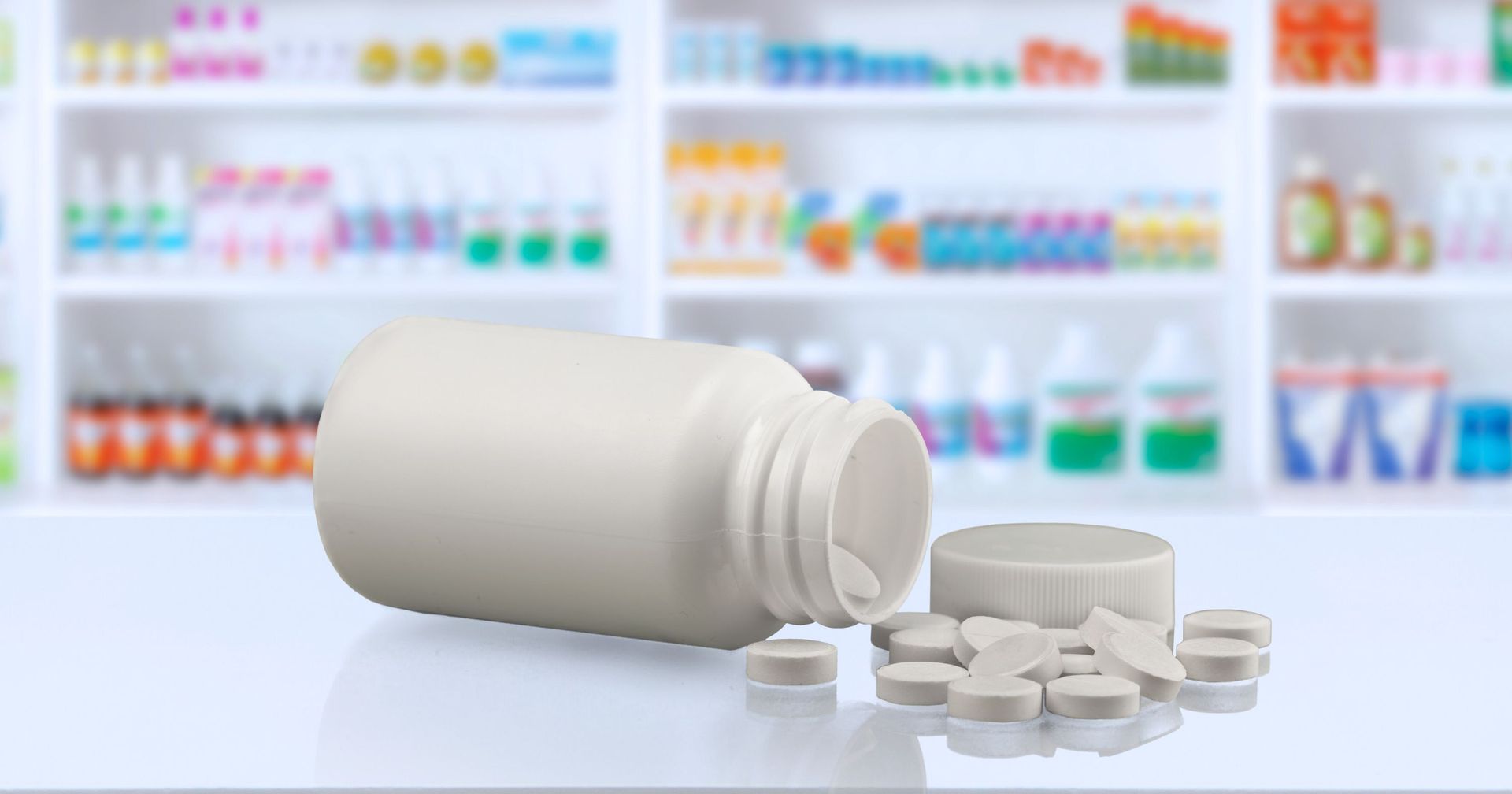
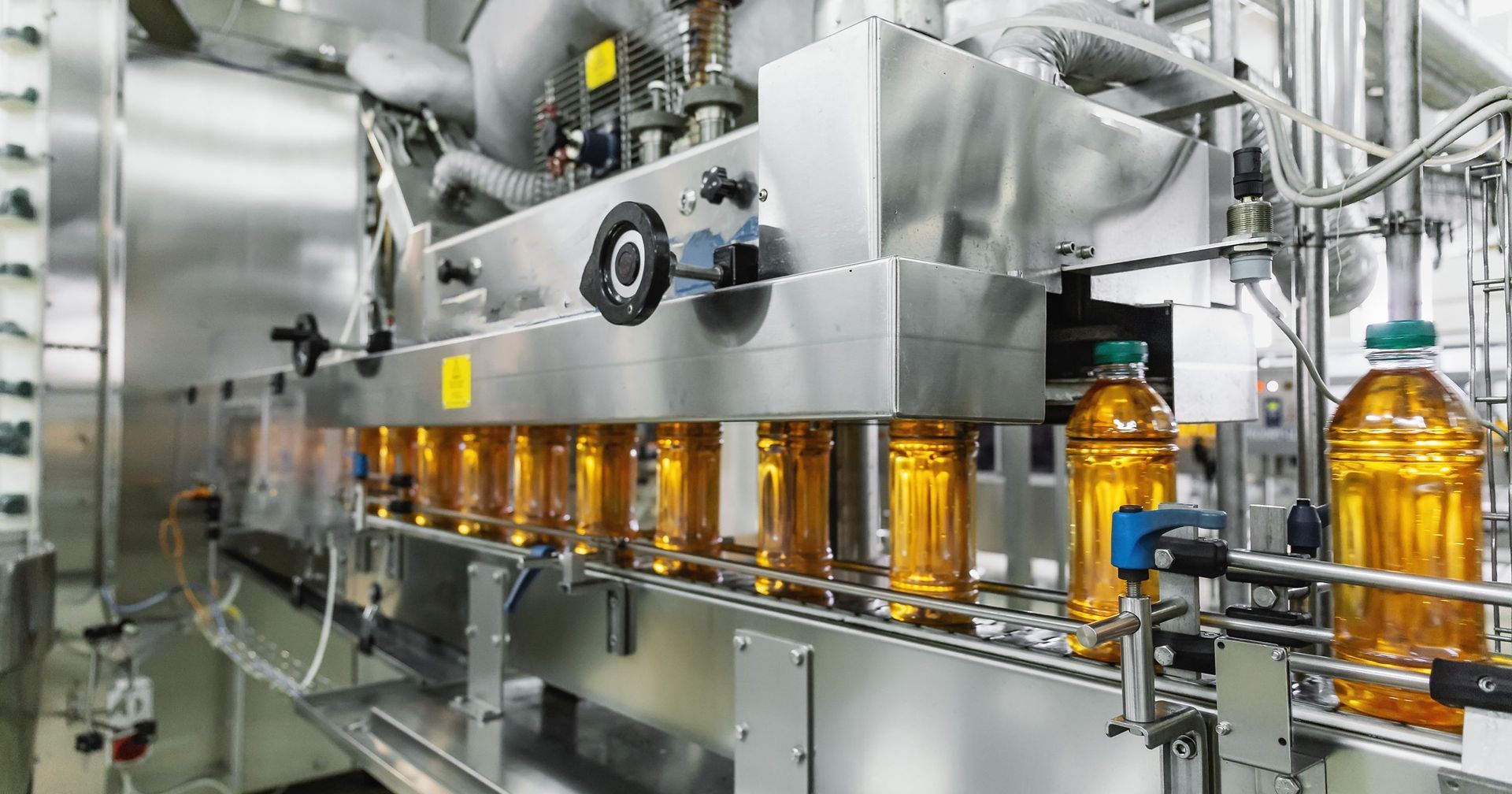

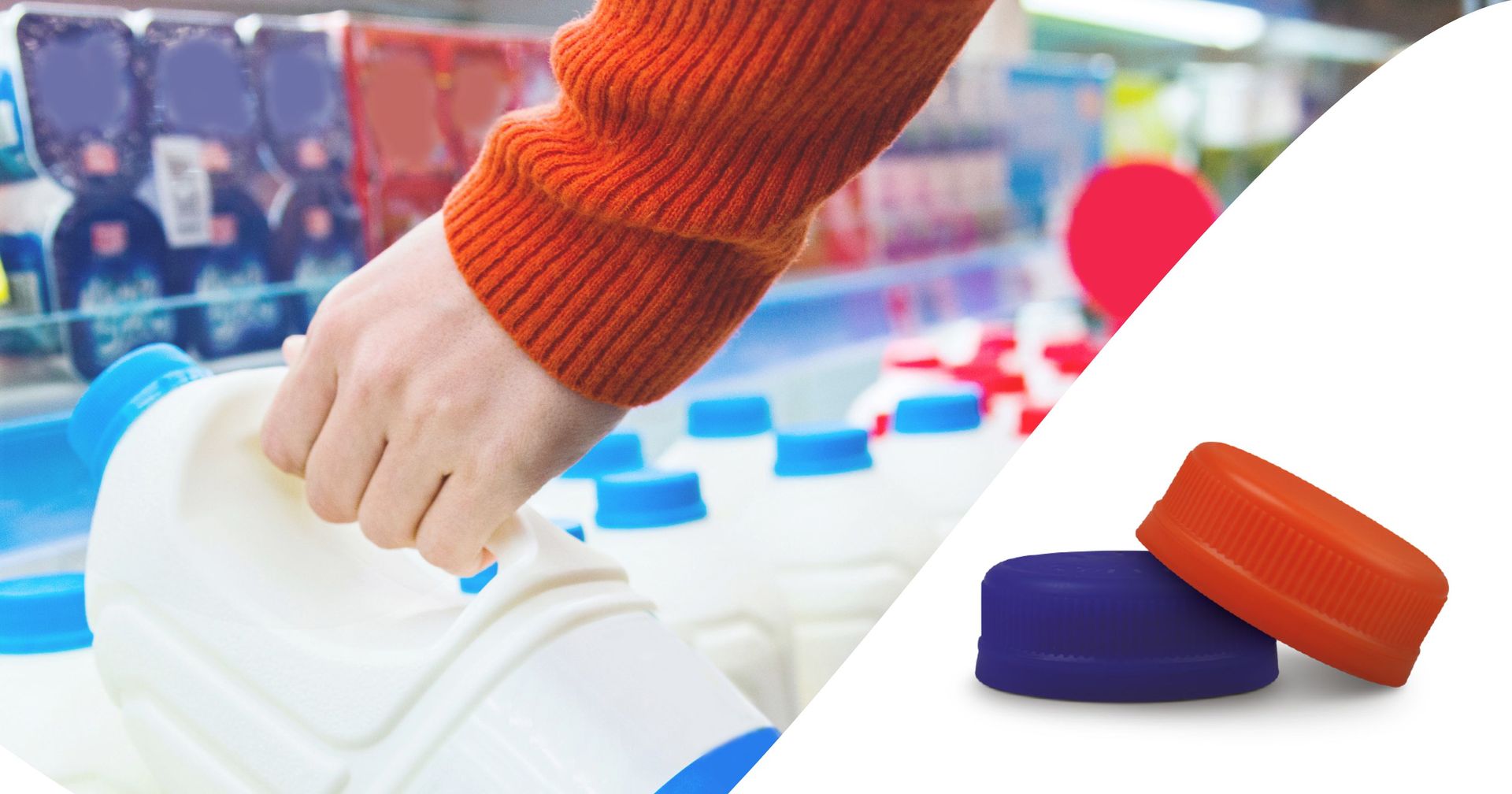
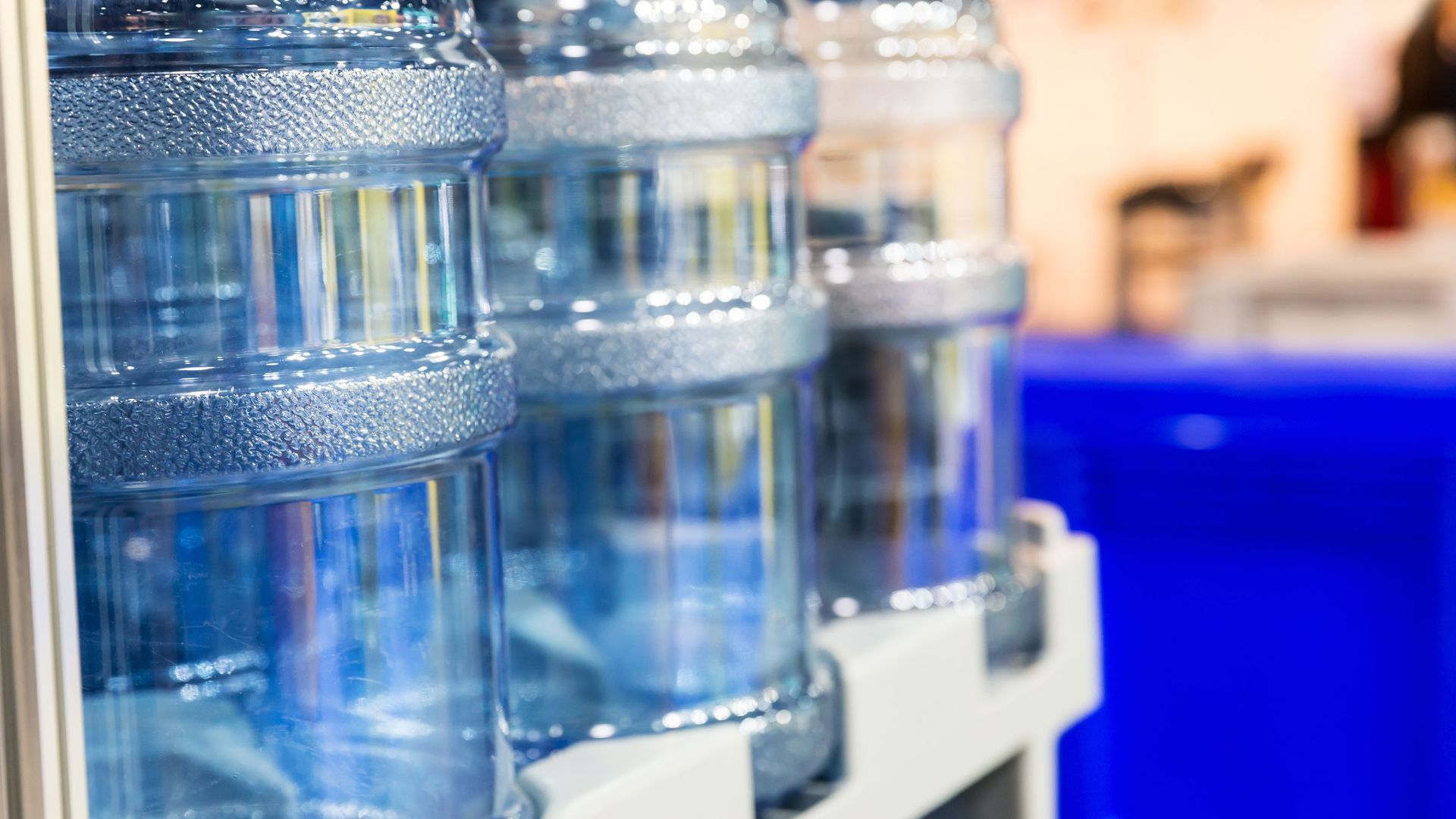
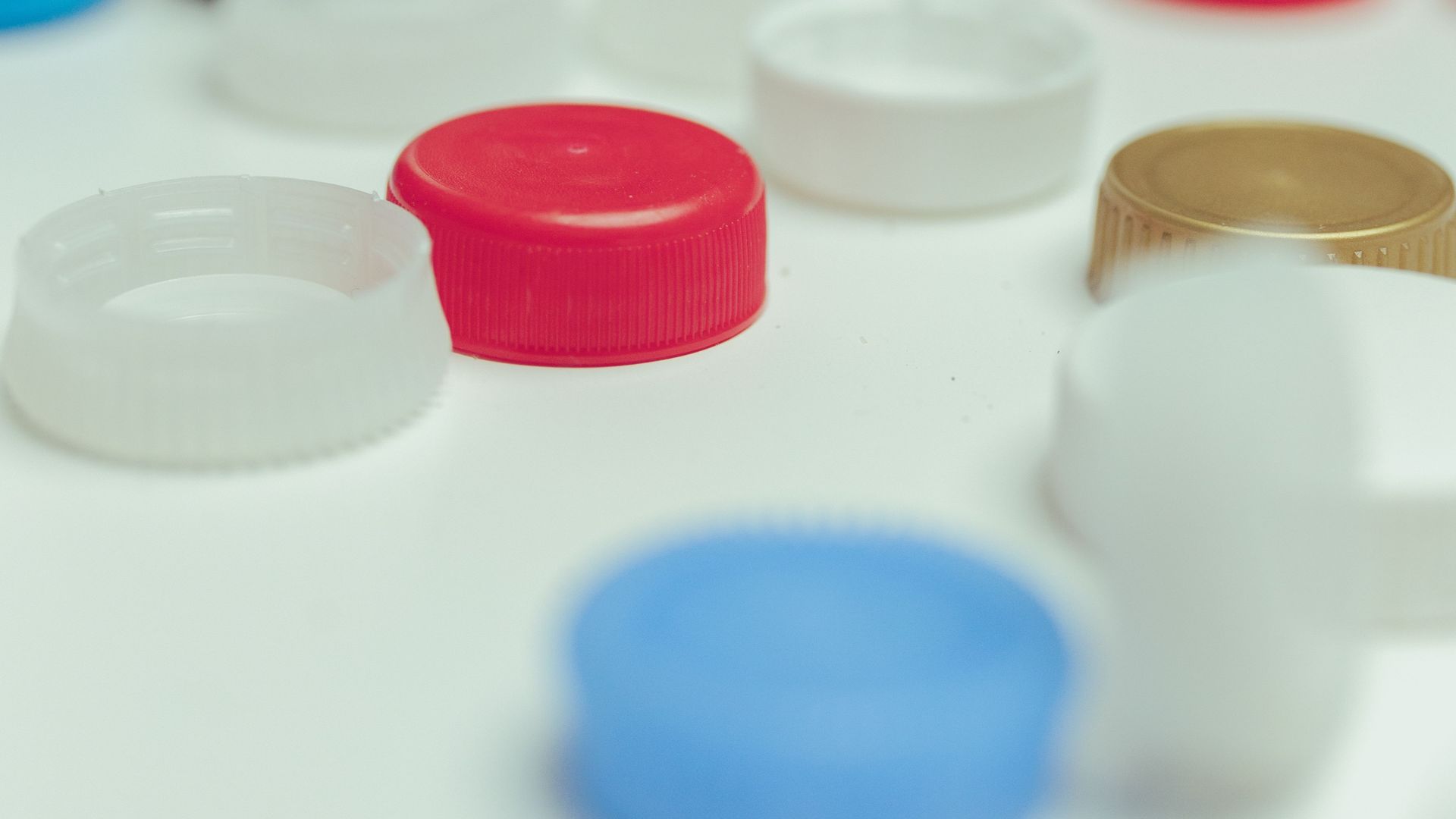
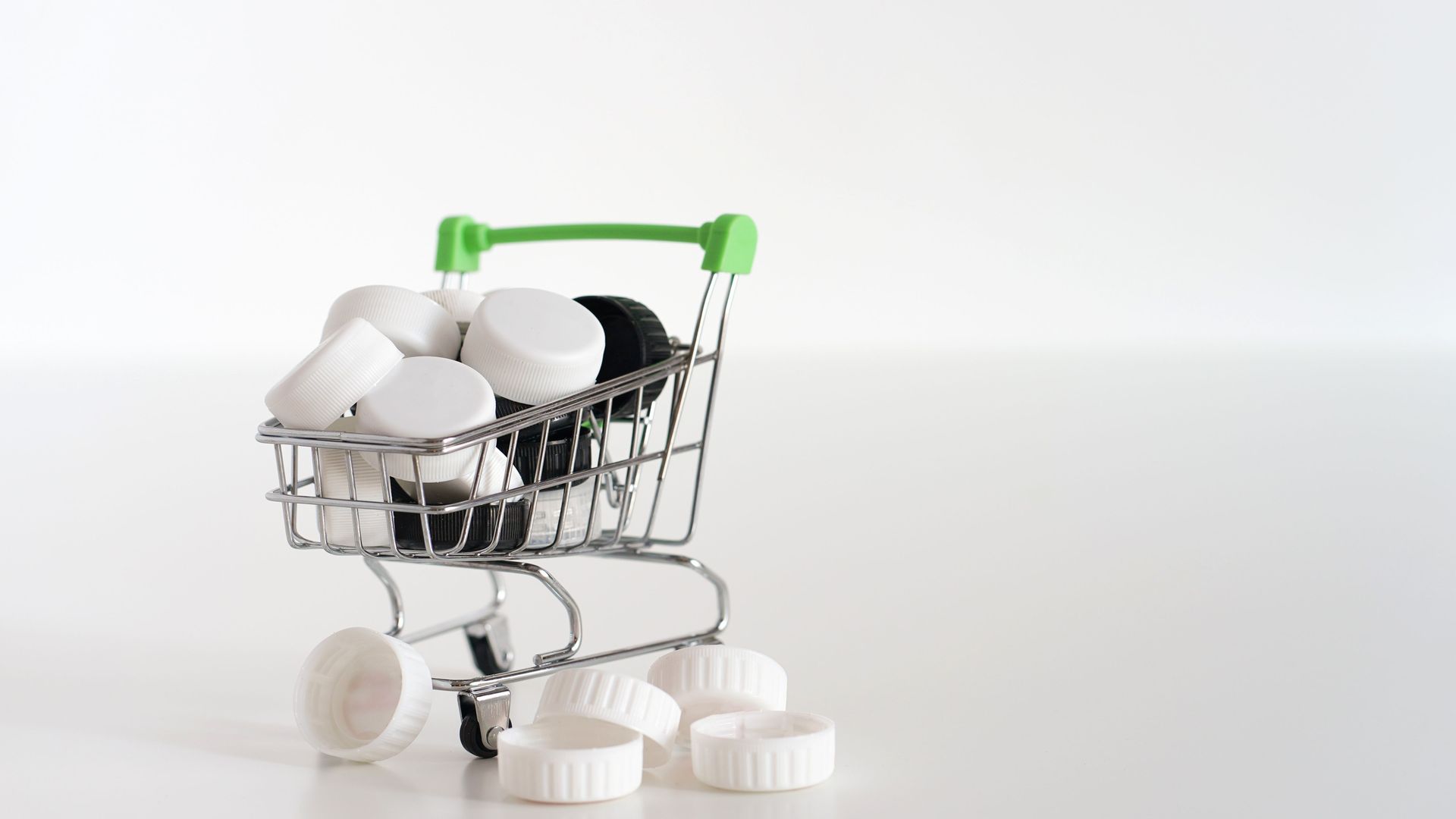
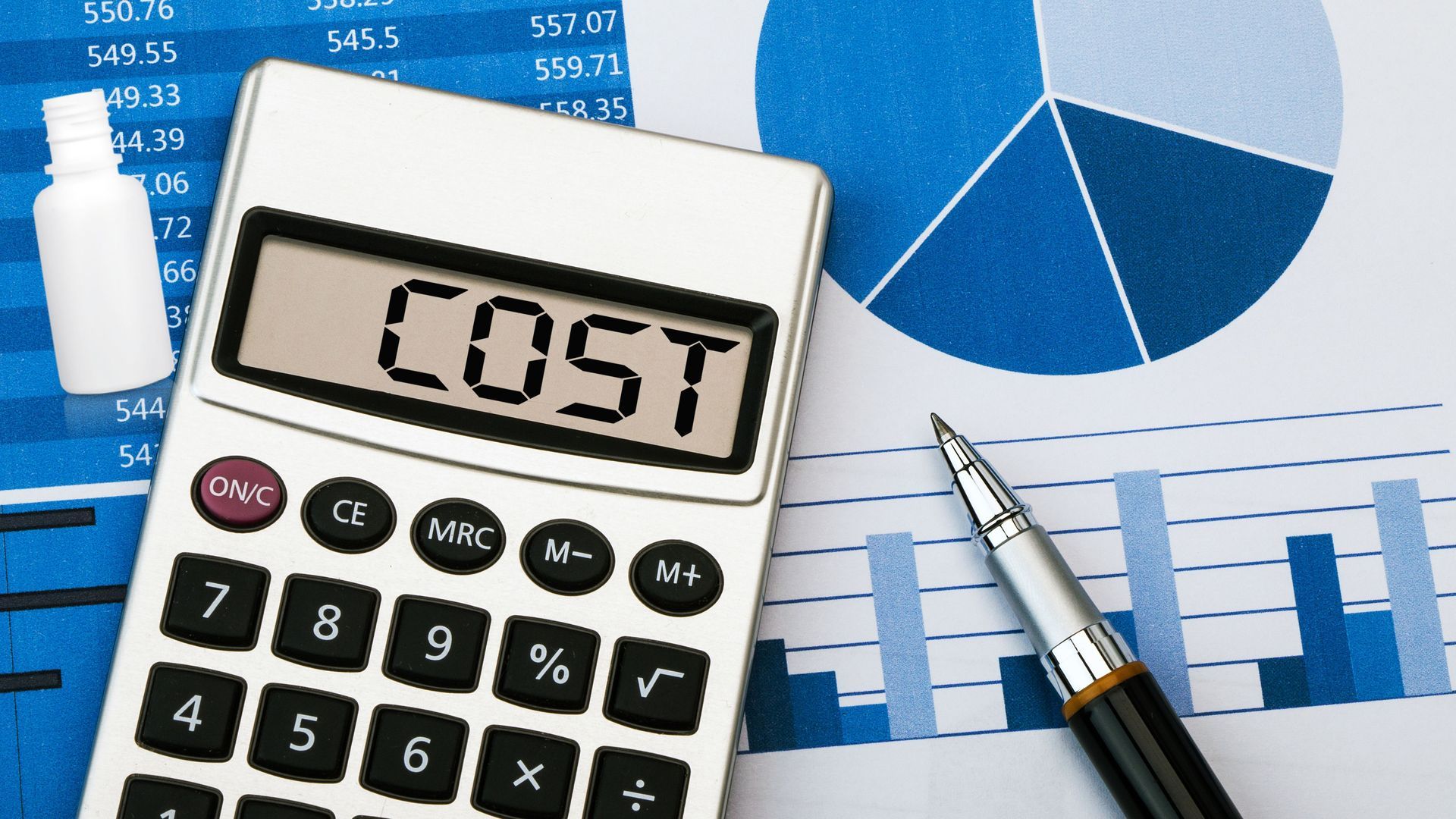