Compression Molding Process for the Manufacture of Compression Caps
Juan Carlos Cuevas • 22 de mayo de 2023
Next, let’s talk about the Compression molding process, a method used to make Compression Caps for different Industries such as Pharmaceutical, Food and Cosmetics.
Compression molding, used to make Compression Caps, is a molding method in which molding material, usually preheated, is placed in the open mold cavity. The mold is closed, heat and pressure is applied to force the material into all areas of the mold, while the heat and pressure is maintained until the molding material has cured. The process is used on thermosetting resins (as opposed to thermoplastic resins) in a partially cured state, either in the form of pellets, putty, or preforms. Compression molding is a high-pressure method, ideal for manufacturing Compression Caps for the previously mentioned industries.
It is one of the lowest cost molding methods compared to other methods such as injection molding, on the other hand, little material is wasted, giving you an advantage when working with expensive compounds. Less fiber length degradation occurs in this process compared to injection molding.
The molds for this process are generally simpler than those for its counterpart, injection molding. There are no hot-runners or feed systems in a compression mold and simpler shaped parts are processed because thermosets have a lower flow capacity. However, accessories are needed to heat the mold which can be done by electrical resistance, steam or hot oil circulation. Compression molds can be classified as manual molds used for test runs; semi-automatic, in which the pressing stage is followed by a programmed cycle, but the operator manually loads and unloads the press; and automatic which operates under fully automatic pressing cycles (including automatic loading and unloading).
Advantages of compression molding:
• Fluid over small distances: lower internal stresses.
• Simple design of moulds, since there are no entrances and channels.
• Allows molding of complex parts
• Good surface finish (in general)
• Relatively low material waste
• Little variation of dimensional characteristics
Plasscon manufactures, through this process, caps for the pharmaceutical, food and cosmetic industries, with cutting-edge technology and under strict quality standards.
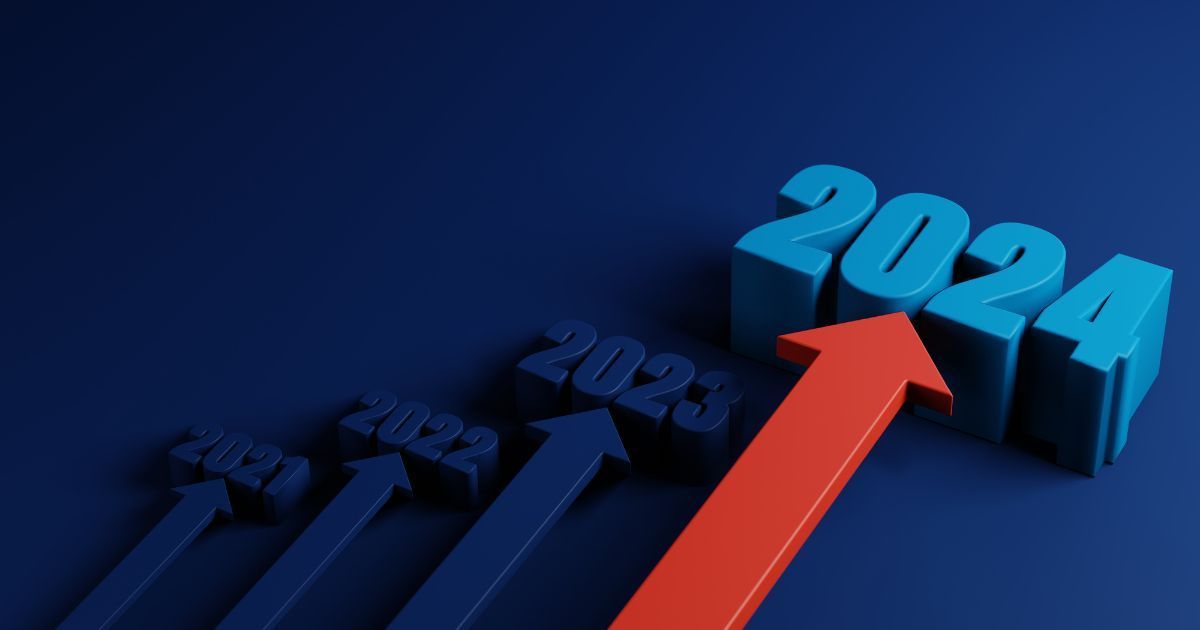
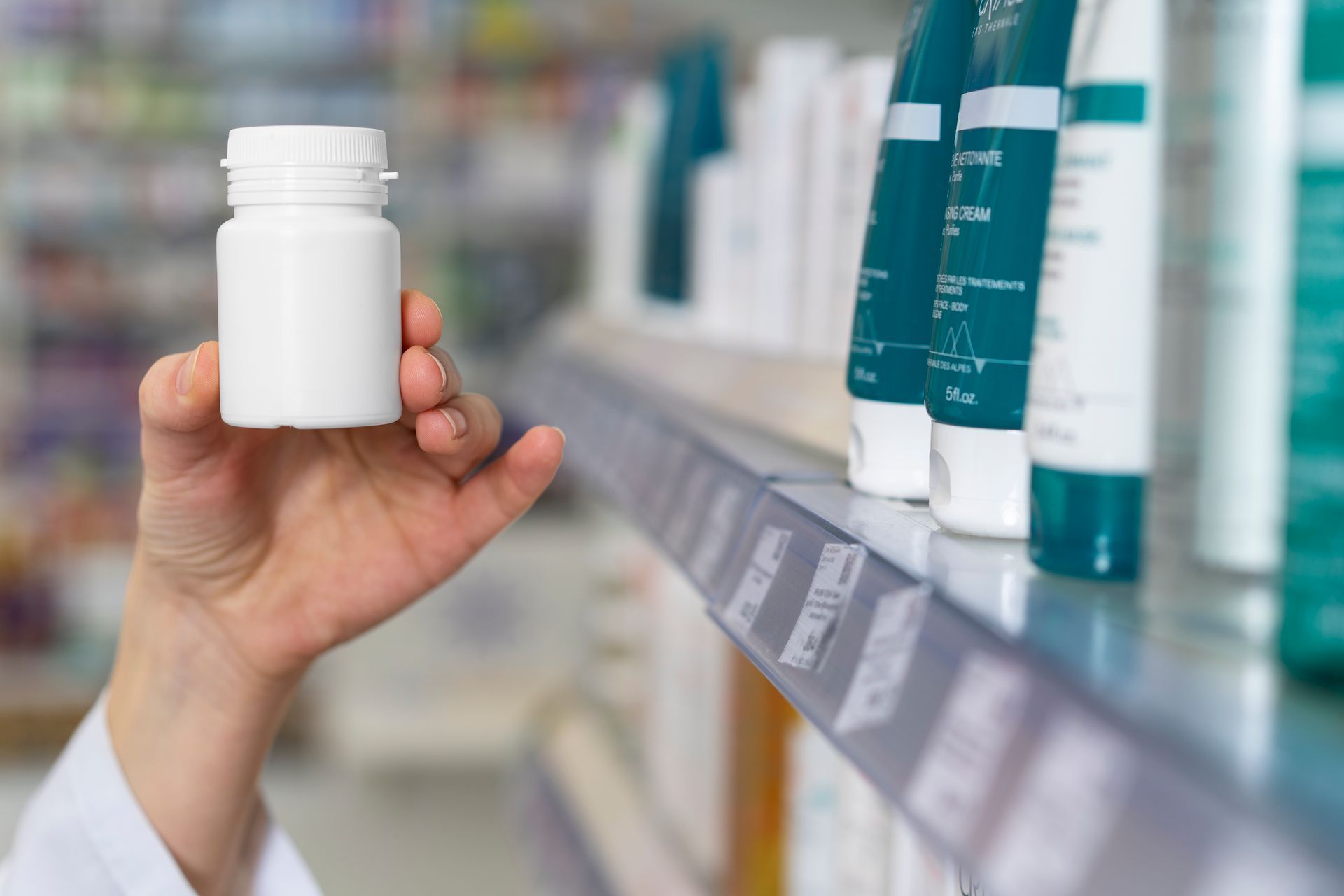
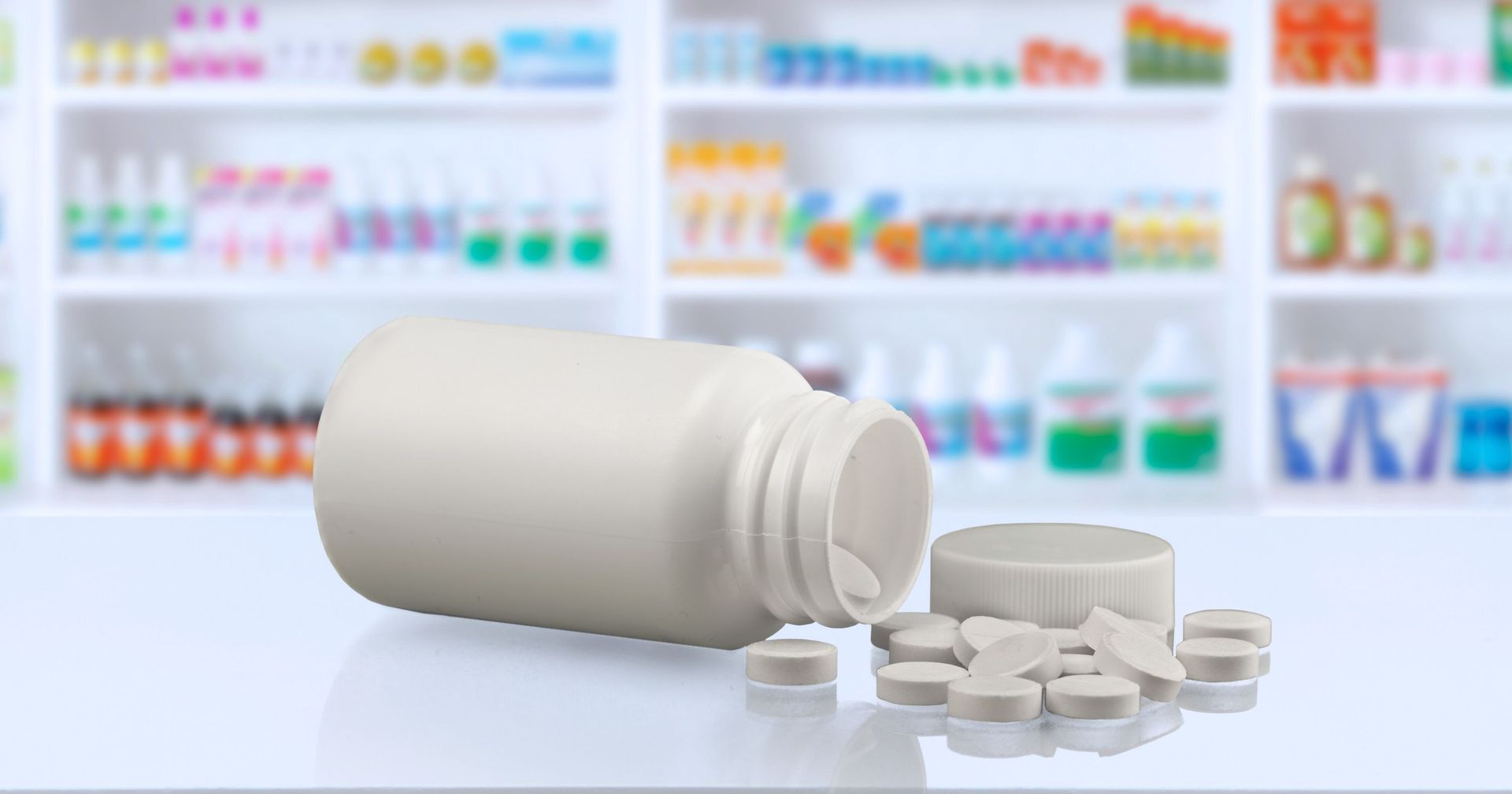
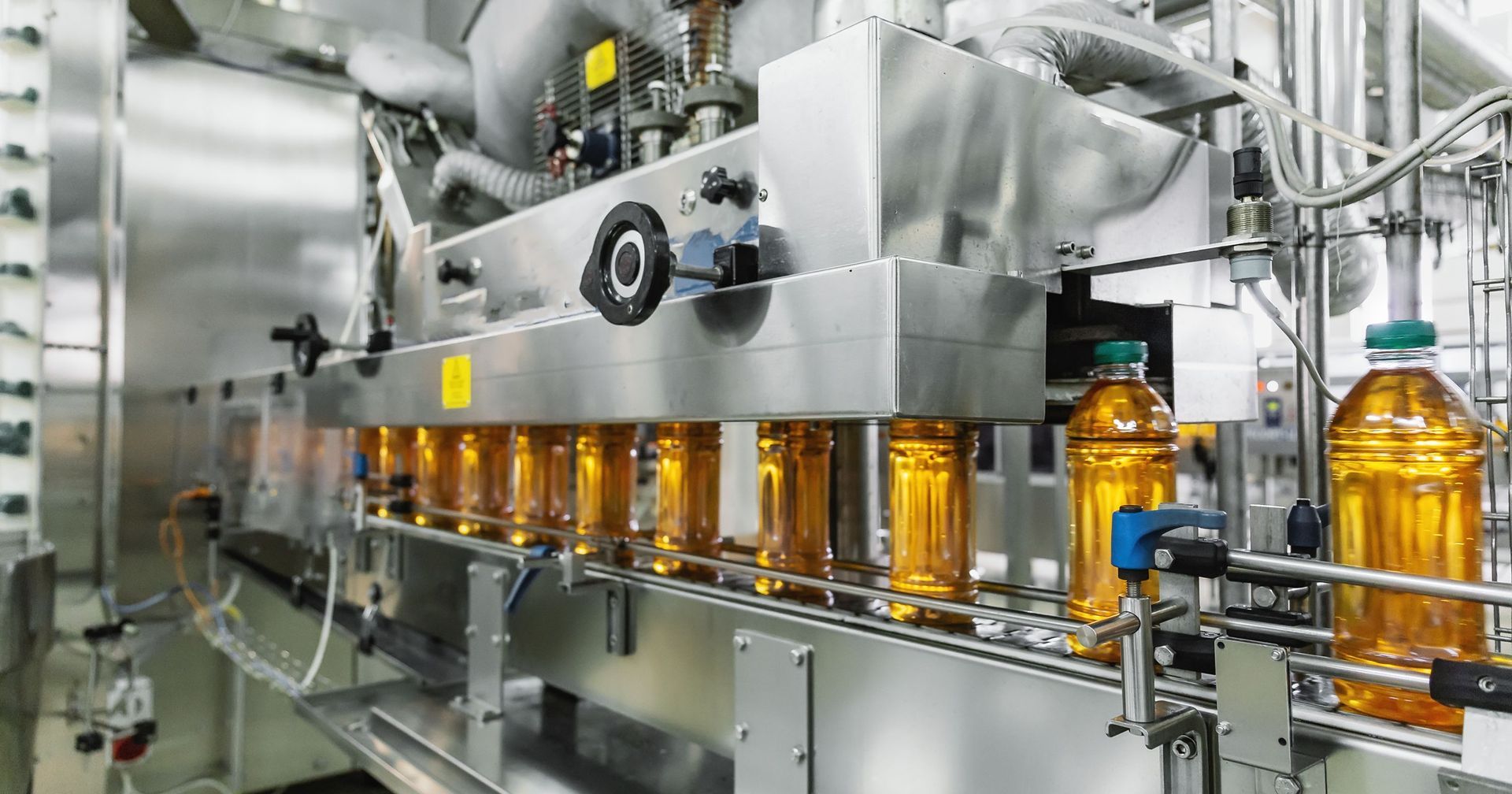


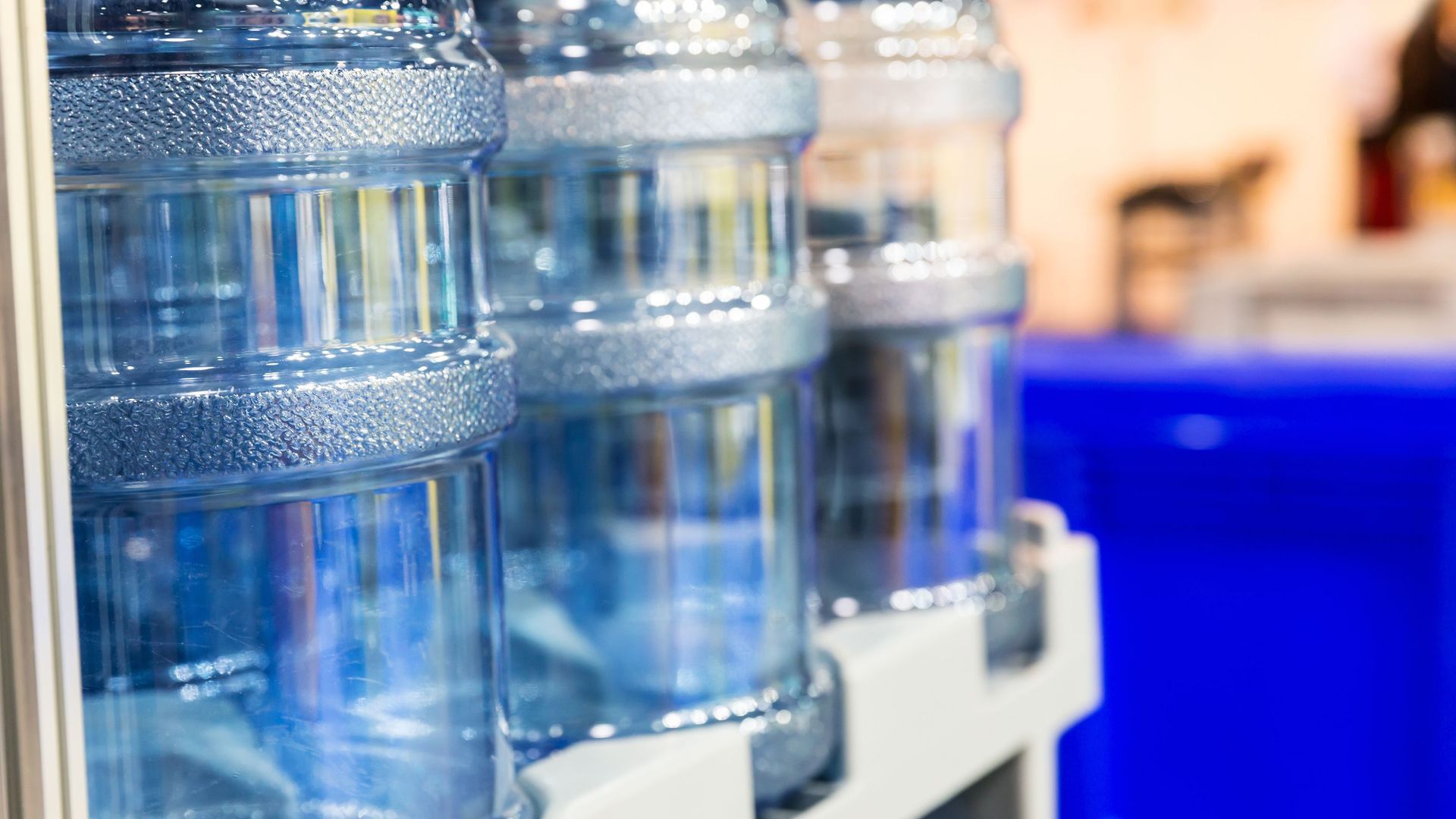
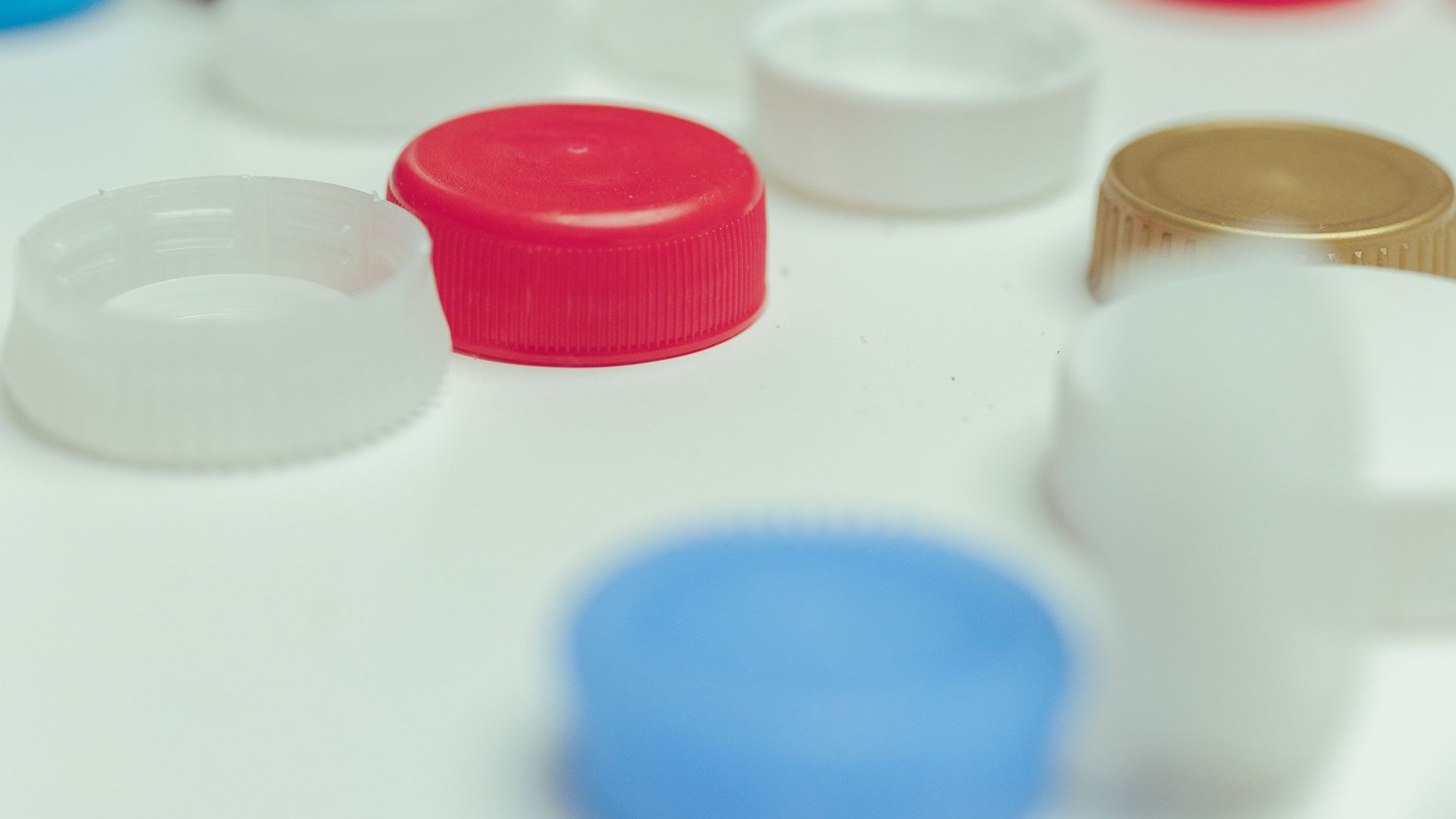
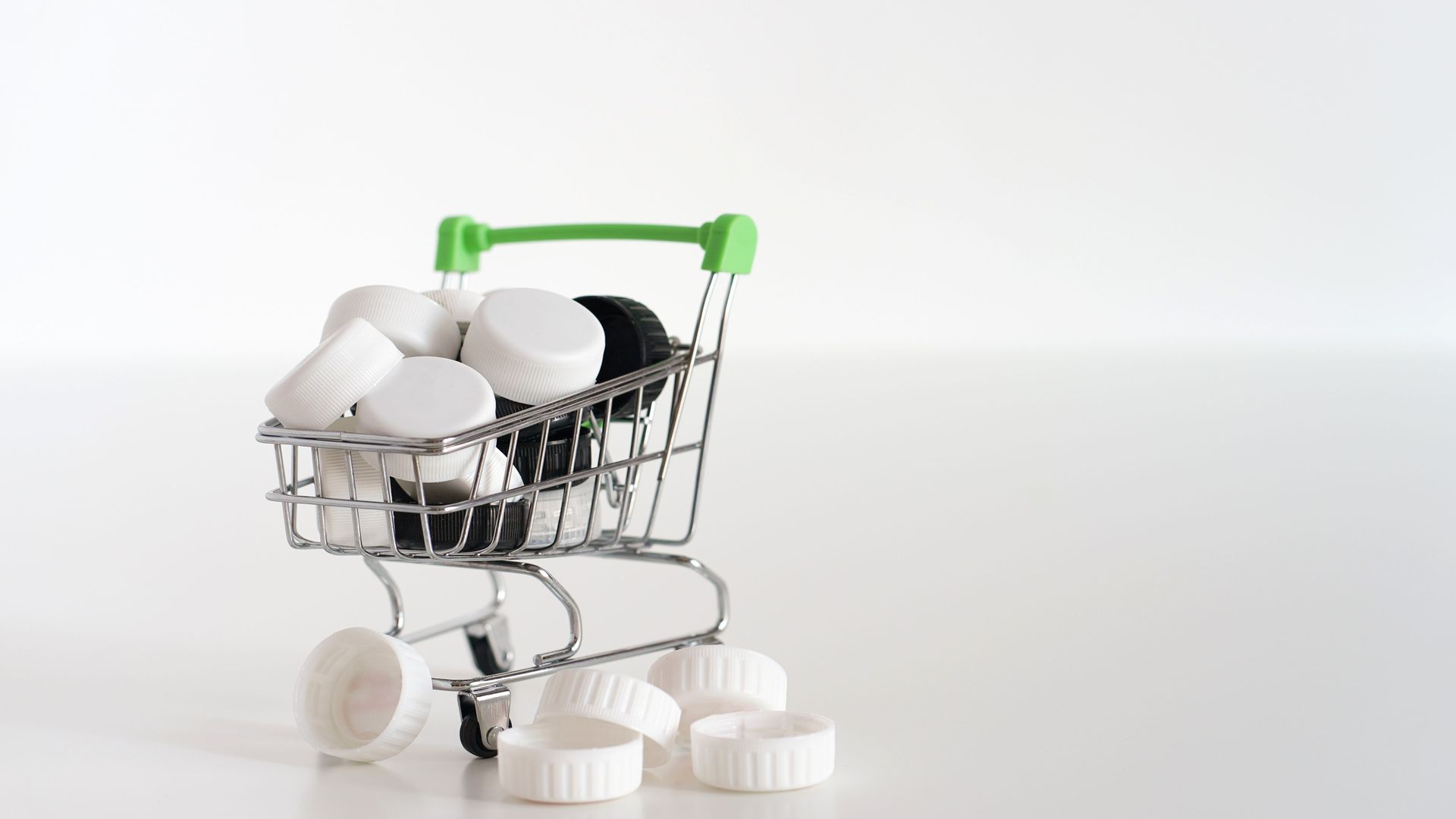