Injection Process to Manufacture Lids, Caps, Closures, Stoppers, Inserts and Dosing Cups for the Pharmaceutical Industry
Juan Carlos • 8 de junio de 2023
Continuing with the different processes by which it is possible to manufacture different plastic products for the industries: pharmaceutical, food and cosmetics, we will talk about the Injection process, especially for the manufacture of Lids, Caps, Closures, Inserts and Dosing Cups.
Let’s learn a little about how plastic parts for the pharmaceutical industry are manufactured, such as: of Lids, Caps, Closures, Inserts and Dosing Cups through the injection process. The plastic injection technique consists of molding an element (in this case Lids, Caps, Closures, Inserts and Dosing Cups) thanks to a mold that houses the piece. Polymers are injected into the mold under pressure through a nozzle and constant pressure is maintained to fill alls the spaces, crooks and cranies in the mold and then the part cools, giving it its final shape. Once the process is finished, the mold opens to drop the finished product onto a tray.
How is the melt of the polymer achieved so that it enters the mold? Well, in order to melt the polymer, a complex process must be followed that must be in complete coordination with the injection to control the temperature, which must be exact, quantity and synchronization in time. For this reason, although injection may seem like a simple process as it is currently the most widely used, the entire transformation requires exhaustive control.
In the transformation of plastic by injection, the molds are the ones that give the desired shape to the piece or pieces (in this case Lids, Caps, Closures, Inserts and Dosing Cups for the pharmaceutical industry), since a mold can have a single cavity, to inject one piece per cycle, or several cavities. In the process prior to the injection of the plastic into the mould, some powerful heat element that are located in the spindle chamber are responsible for the plastic melting, homogenizing and plasticizing properly and, subsequently, being injected into the mold to the manufacture of the final product.
As we have mentioned before, this process works in perfect synchronization as otherwise, large volumes of work would not be achieved. Remember that the pieces must be exact, so this synchronization cannot fail in all fundamental aspects: temperature, quantity, solidification, etc.
Below are the reasons why the fundamental elements mentioned before for the manufacture of pharmaceutical products through plastic injection are key:
Temperature: This must be controlled very precisely to ensure that the injected polymer fuses correctly. It must be remembered that, for the injection process, it is necessary to heat up prior to injection and then cool down to achieve the desired piece. In the cooling process we will also depend on the type of piece required (size, shape, quantity,...). Therefore, temperature is one of the most important elements in the transformation process.
Pressure: The pressure exerted by the process is also a very important element for the raw material to cool properly, adapting its shape to that of the mold used. Exerting strong and constant pressure is another of the most important requirements of the process.
Speed: The polymer already molten through the resistance of the cavities goes directly to the mold in a matter of seconds. This process must be immediate and fast since, from the first moment the material enters the mold, its cooling process begins. For this reason, the passage to the mold must be very fast and controlled.
Plasscon manufactures Lids, Caps, Closures, Inserts and Dosing Cups, through this process, with cutting-edge technology and under strict quality standards.
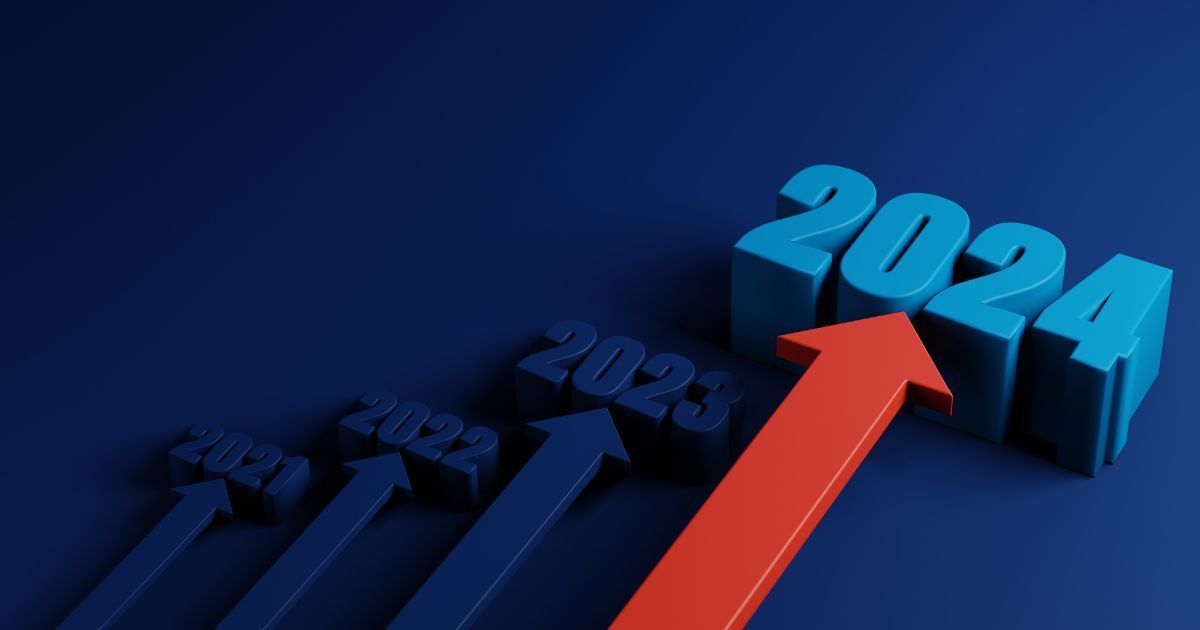
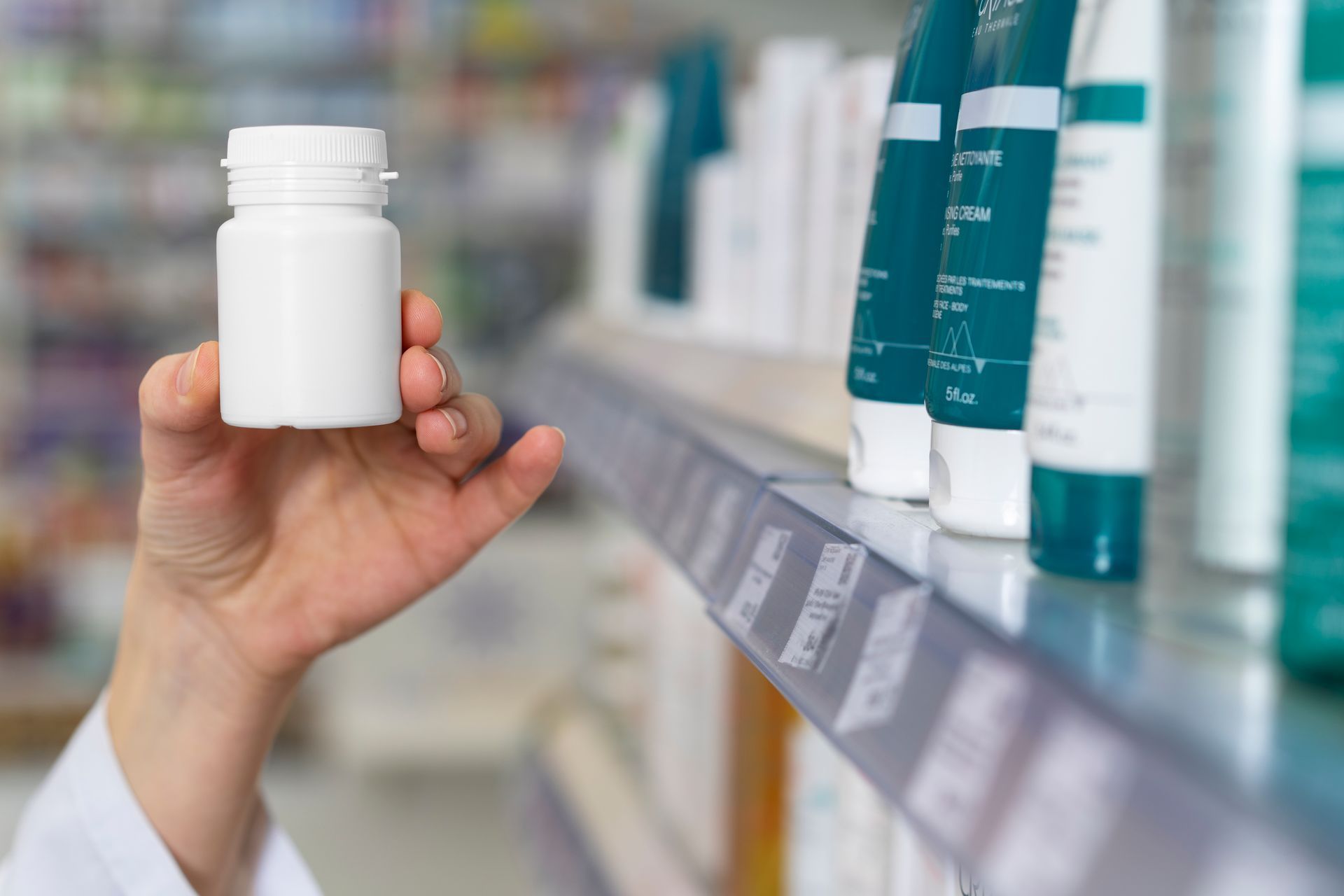

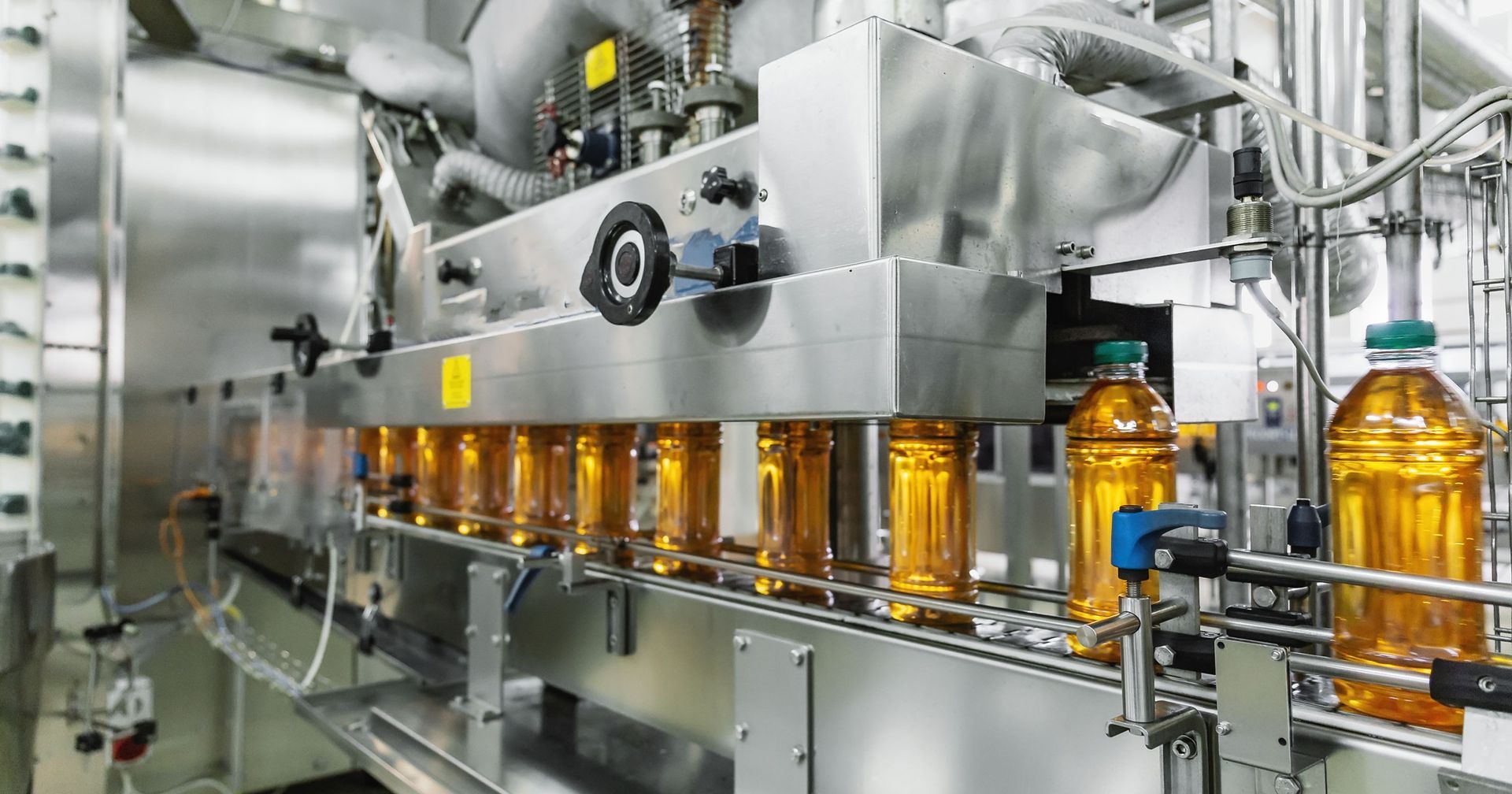
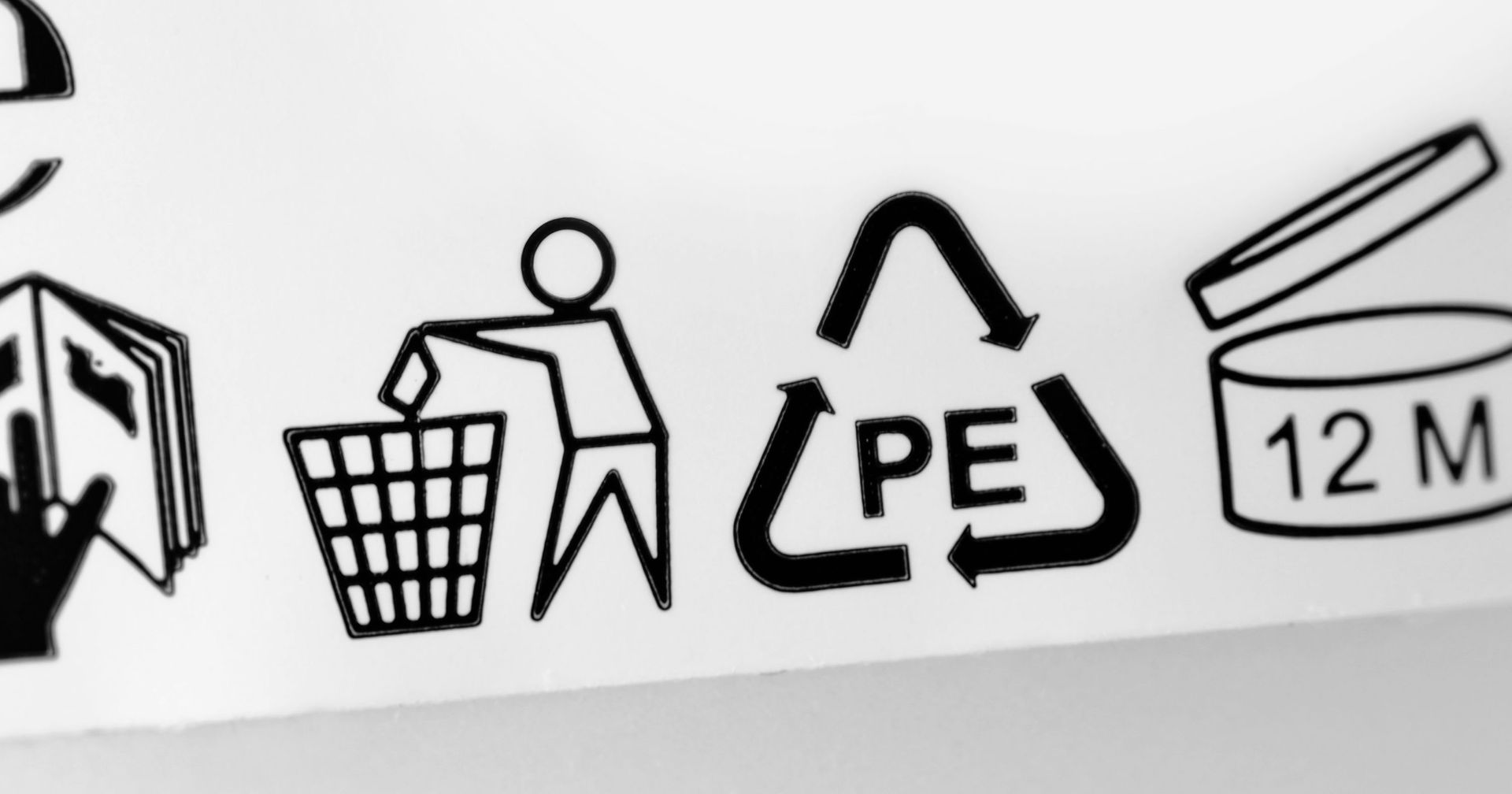
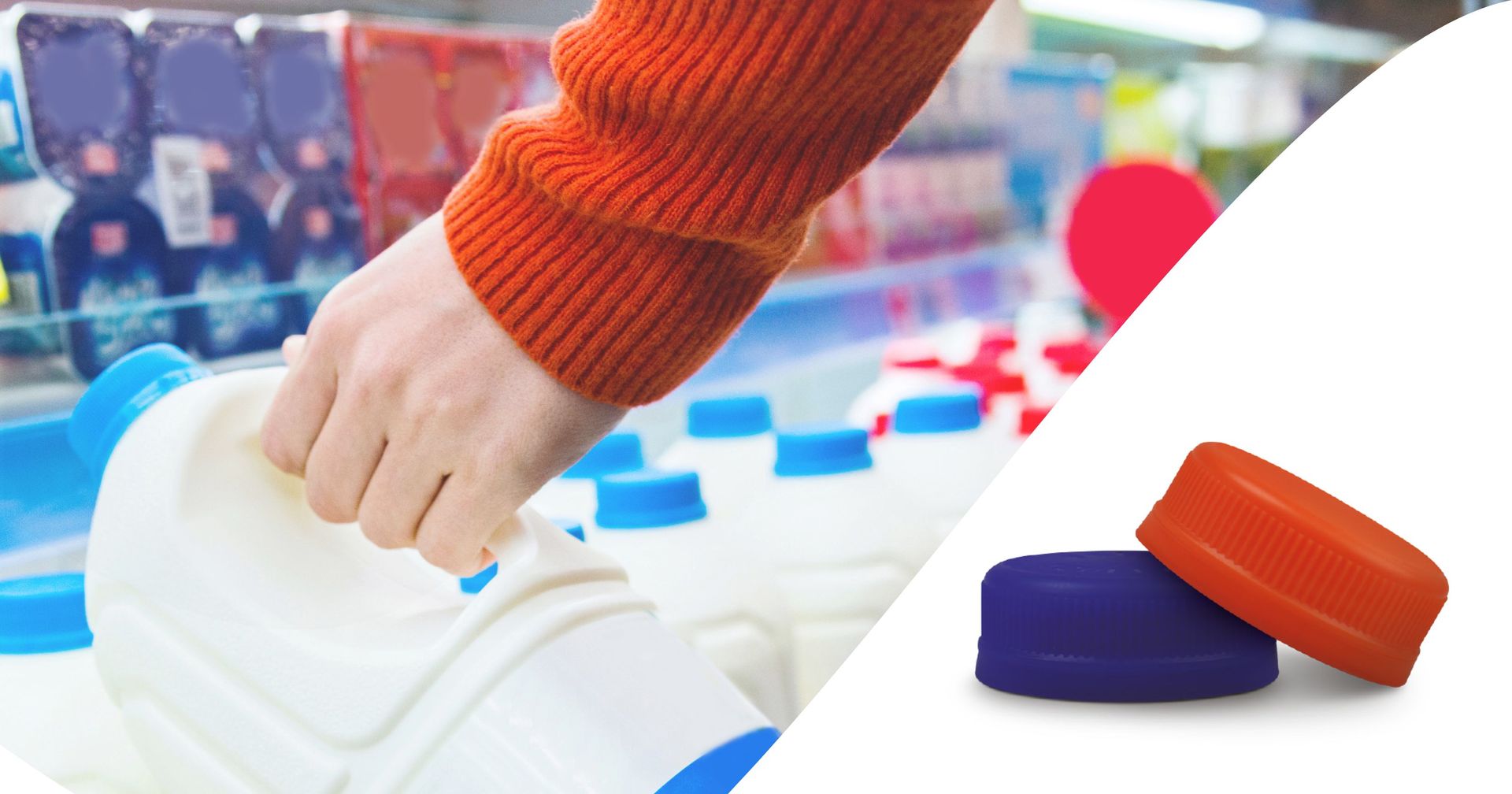
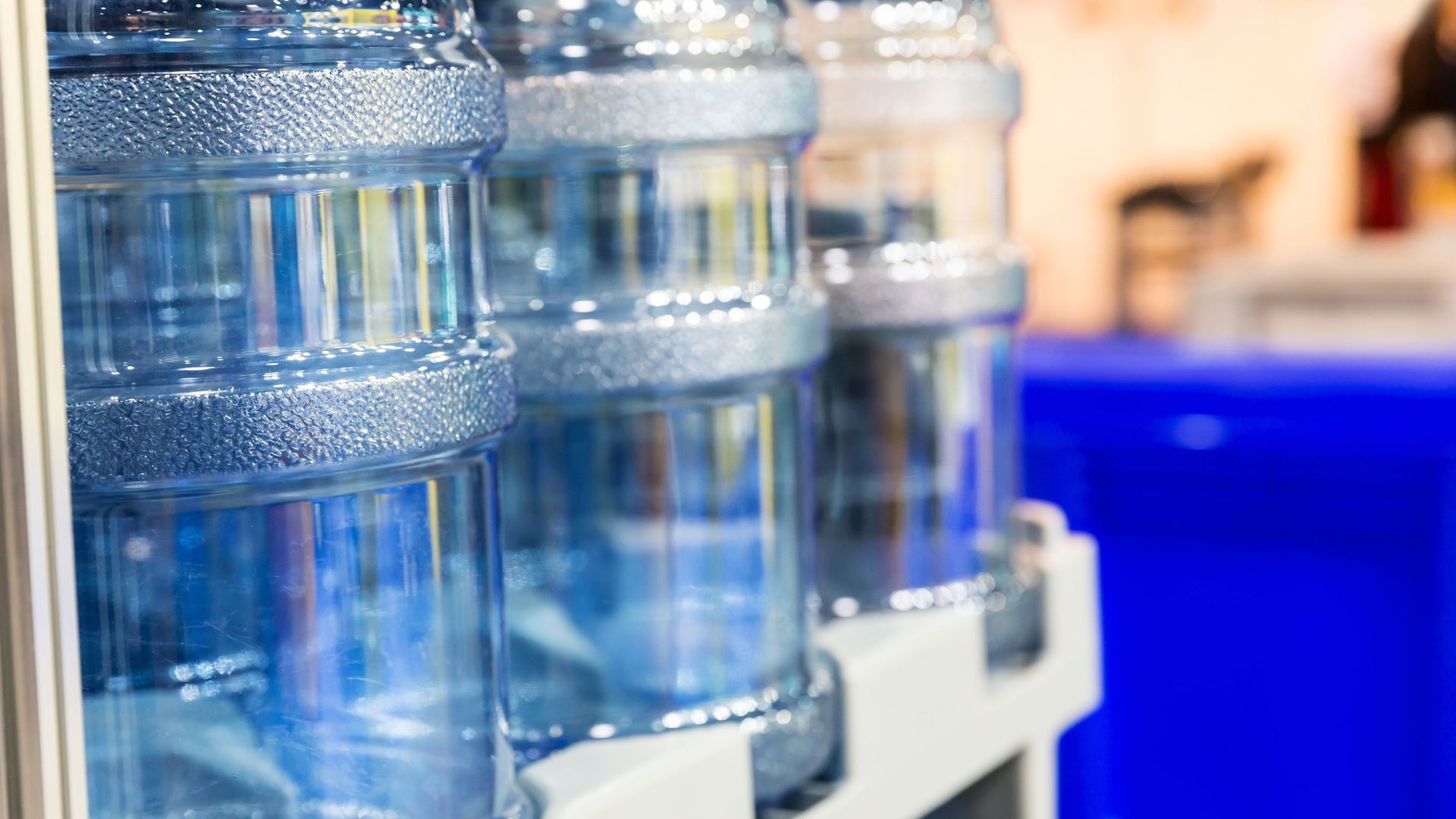
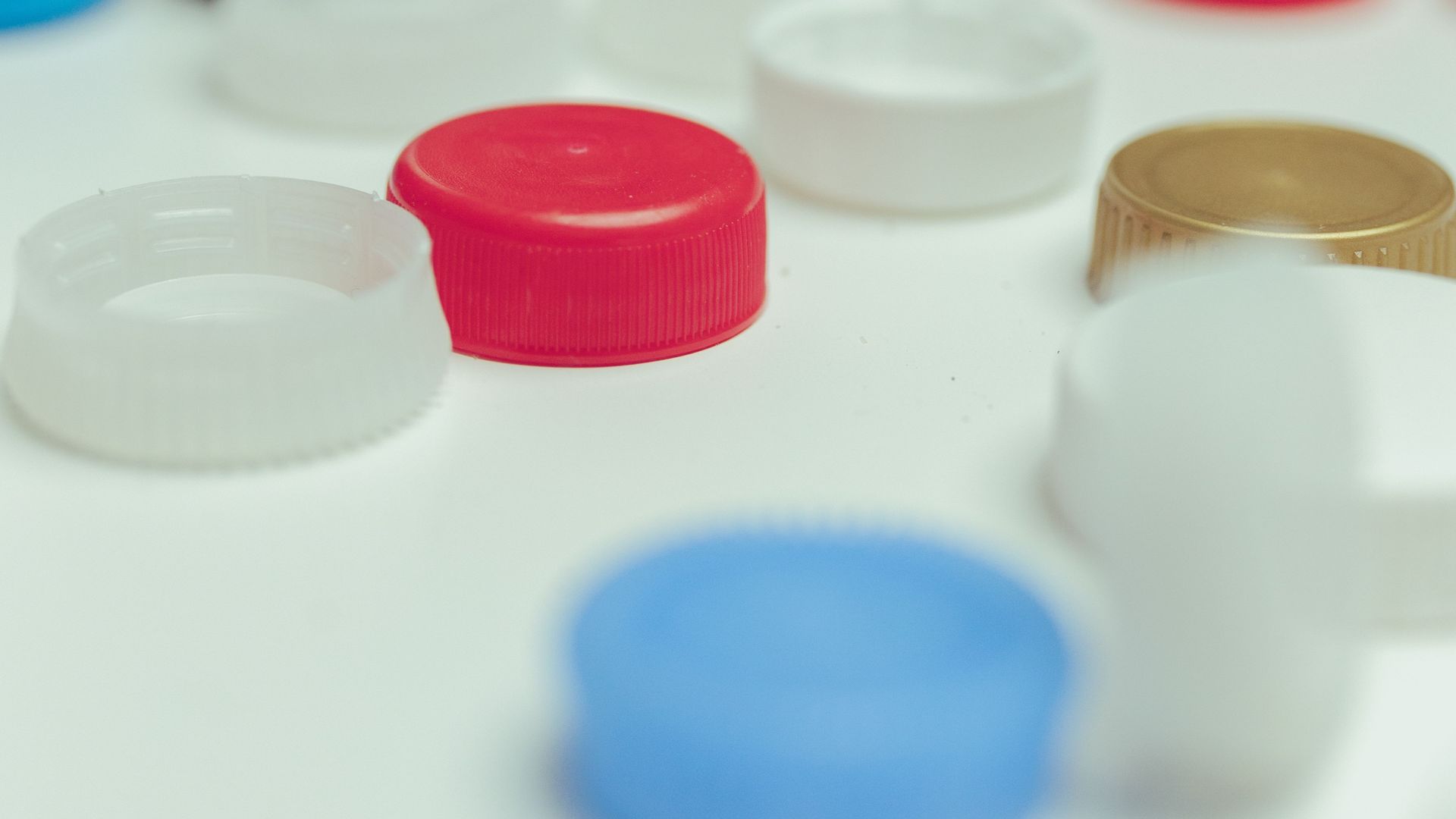
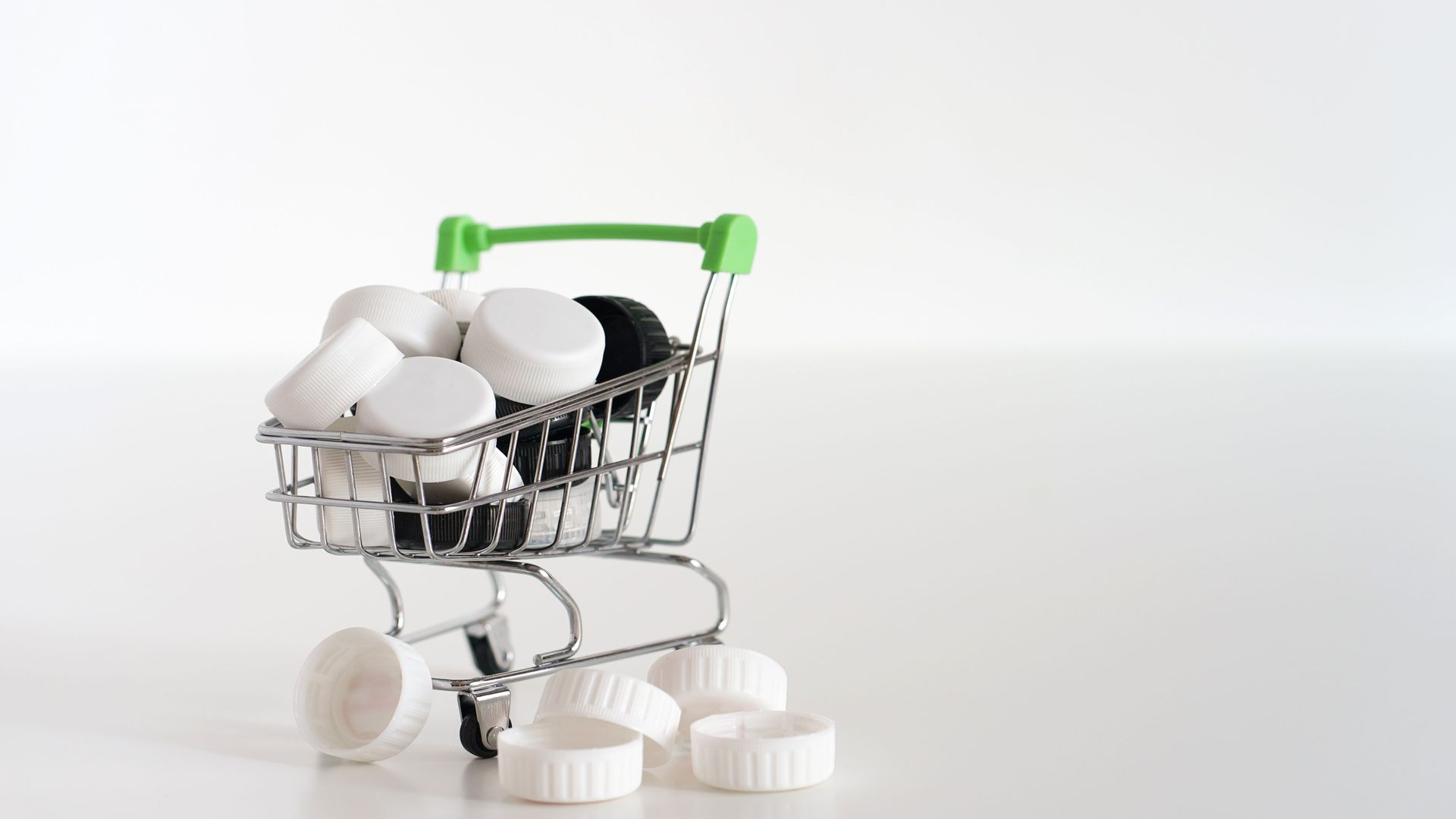